Precision Die Casting Part: A Cost-Effective Solution for Manufacturing
By:Admin
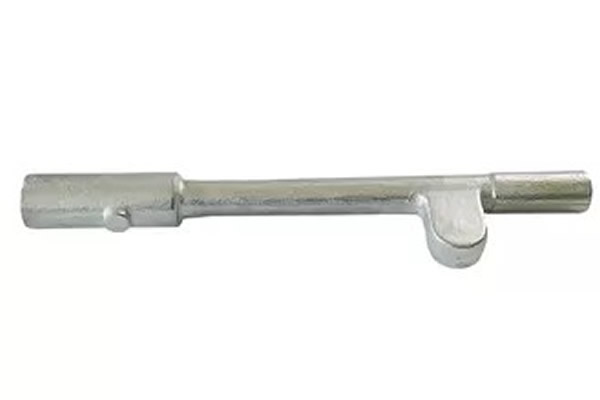
In the world of modern manufacturing, die casting has revolutionized the production process of various metal parts and components. Die casting is a process which involves the use of molten metal that is forced into a mold cavity under high pressure. This results in the creation of intricate and precise components, also known as die casting parts, that are crucial in a wide range of industries including automotive, aerospace, electronics, and more.
One company that has been at the forefront of die casting technology is {}. With over 20 years of experience in the industry, {} has been providing high-quality die casting parts to their global clientele. Their state-of-the-art facilities and commitment to innovation have made them a trusted name in the industry.
Die casting parts are used in a multitude of applications, from intricate and lightweight components in the automotive industry to complex and durable parts in the aerospace industry. The versatility of die casting makes it an ideal choice for the production of a wide range of components.
One of the key advantages of die casting is the ability to create parts with high precision and consistency. The use of molds allows for the production of intricate and complex shapes with tight tolerances, ensuring that each part meets the exact specifications required. This level of precision is crucial in industries where even the smallest deviation can have a significant impact on the performance and safety of the final product.
Another advantage of die casting is the ability to produce parts with excellent surface finish and dimensional stability. This is particularly important in industries such as electronics and telecommunications, where the appearance and performance of the final product are of utmost importance. The high pressure used in the die casting process ensures that the molten metal fills every crevice of the mold, resulting in parts with smooth surfaces and fine details.
Furthermore, die casting parts are known for their strength and durability, making them suitable for a wide range of industrial applications. The use of high-quality metals such as aluminum, zinc, and magnesium ensures that the final parts are able to withstand harsh working environments and extreme conditions. This makes die casting an ideal choice for industries where reliability and performance are paramount.
In addition to its functional advantages, die casting also offers cost-effective solutions for the production of complex metal parts. The ability to create multiple identical parts with minimal post-processing and waste makes die casting an efficient and economical manufacturing method. This is especially important for industries that require high volume production of components without compromising on quality.
As a leading manufacturer of die casting parts, {} is committed to meeting the evolving needs of their customers. Their team of skilled engineers and technicians are constantly exploring new technologies and materials to further improve the quality and performance of their die casting parts. By staying at the forefront of industry trends and advancements, {} is able to provide innovative solutions that meet the stringent requirements of today's manufacturing industry.
In conclusion, die casting parts play a crucial role in modern manufacturing, offering a combination of precision, durability, and cost-effectiveness that makes them an ideal choice for a wide range of industries. With companies like {} leading the way in die casting technology, the future looks promising for the continued advancement and innovation in this field.
Company News & Blog
High-Quality Forged Automobile Parts for Enhanced Performance
For over 30 years, {} has been a leading manufacturer and supplier of high-quality forging parts for the automobile industry. With a strong focus on innovation and advanced technology, the company has consistently delivered top-notch products to automotive manufacturers around the world.Recently, {} announced the launch of their new line of forging parts specifically designed for automobiles. These parts are crafted using advanced forging techniques to ensure unparalleled strength, durability, and performance.The automobile industry is constantly evolving, with manufacturers continuously seeking to improve the quality and performance of their vehicles. {}’s new line of forging parts is perfectly positioned to meet these evolving needs.One of the key advantages of {}’s forging parts is their exceptional strength-to-weight ratio. By using advanced forging techniques, the company is able to create parts that are incredibly strong and durable, yet lightweight. This not only contributes to improved fuel efficiency in vehicles but also enhances overall performance.In addition to their strength and durability, {}’s forging parts are also designed to meet the highest standards of precision and accuracy. This ensures seamless integration into automobile components, resulting in smoother operation and overall improved vehicle performance.Moreover, {} has also made significant investments in research and development to ensure that their forging parts are at the forefront of innovation in the automobile industry. The company has employed a team of highly skilled engineers and technicians who are dedicated to pushing the boundaries of forging technology, resulting in products that are truly cutting-edge.{}’s commitment to quality and innovation has not gone unnoticed in the automobile industry. Many leading automobile manufacturers have already integrated {}’s forging parts into their vehicles, citing the exceptional performance and reliability of these parts.With the global shift towards electric and autonomous vehicles, the demand for high-quality forging parts in the automobile industry is only expected to grow. {} is well-positioned to meet this demand, with the company’s advanced manufacturing capabilities and commitment to innovation.Furthermore, {}’s dedication to sustainability is another factor that sets them apart in the automobile industry. The company has implemented environmentally friendly practices in their manufacturing processes, ensuring that their forging parts have minimal impact on the environment.In conclusion, {}’s new line of forging parts for automobiles represents a significant step forward for the company and the automobile industry as a whole. With their unwavering commitment to quality, innovation, and sustainability, {} is poised to continue leading the way in providing the automotive industry with top-of-the-line forging parts.
High-Quality 7075 Forging: A Guide to 7075 Forging Process
7075 Forging: The Future of Aerospace ManufacturingThe aerospace industry is constantly evolving, with a growing demand for lighter, stronger, and more durable materials to meet the needs of modern aircraft. One material that has been gaining traction in the industry is 7075 forging, a high-strength aluminum alloy that offers a wide range of benefits for aerospace manufacturing. 7075 forging has become the material of choice for many aerospace applications due to its exceptional strength-to-weight ratio, corrosion resistance, and ability to withstand high stress and fatigue. These properties make it an ideal choice for critical components such as aircraft wings, fuselage, and landing gear.One company at the forefront of 7075 forging is {}, a leading manufacturer of high-performance materials for aerospace and other advanced applications. With state-of-the-art facilities and a team of experts in metallurgy and engineering, {} has been able to push the boundaries of what is possible with 7075 forging, delivering innovative solutions for the aerospace industry.One of the key advantages of 7075 forging is its lightweight nature, which can significantly reduce the overall weight of an aircraft without compromising its structural integrity. This is particularly important in today's aerospace industry, where fuel efficiency and environmental sustainability are top priorities. By utilizing 7075 forging, aircraft manufacturers can enhance fuel efficiency, reduce emissions, and ultimately lower operating costs.In addition to its lightweight properties, 7075 forging also offers exceptional strength and durability, making it an ideal material for withstanding the harsh conditions of aerospace environments. Its high tensile strength and resistance to fatigue make it well-suited for withstanding the stresses and strains of flight, ensuring the safety and reliability of aircraft components.Another key benefit of 7075 forging is its excellent corrosion resistance, which is crucial for maintaining the longevity and performance of aerospace components. This ensures that aircraft components made from 7075 forging can withstand the rigors of long-term exposure to harsh environmental conditions, such as high altitudes, temperature fluctuations, and exposure to saltwater and other corrosive elements.With the growing demand for advanced materials in the aerospace industry, the future of 7075 forging looks promising. As aircraft manufacturers continue to seek materials that can meet the stringent requirements of modern aerospace applications, 7075 forging is expected to play a crucial role in shaping the future of aerospace manufacturing.In conclusion, 7075 forging is revolutionizing the aerospace industry, offering a winning combination of lightweight, high-strength, and corrosion-resistant properties that make it an ideal choice for critical aerospace applications. With {} at the forefront of innovation in the field, the future of aerospace manufacturing looks brighter than ever, as 7075 forging continues to push the boundaries of what is possible in the aerospace industry.
High-Quality Carbon Steel Casting for Industrial Applications
Carbon Steel Casting Company, a leading provider of high-quality carbon steel casting solutions, has announced its expansion into new markets with the introduction of a range of innovative products designed to meet the growing demand for carbon steel components in various industries.The company, which has a strong reputation for delivering superior carbon steel casting products, has been at the forefront of the industry for over a decade. With state-of-the-art facilities and a team of experienced professionals, Carbon Steel Casting Company has built a solid foundation in the market, providing reliable and efficient solutions to its customers.The expansion into new markets comes as a result of increasing demand for carbon steel components in industries such as automotive, construction, and energy. The company's commitment to delivering top-quality products and its ability to meet the specific requirements of its customers have positioned it as a trusted partner in the industry.One of the key factors that set Carbon Steel Casting Company apart from its competitors is its advanced manufacturing processes and cutting-edge technology. The company's modern facilities are equipped with the latest casting equipment and machinery, allowing for the production of complex, high-precision components with exceptional accuracy and consistency.In addition to its advanced manufacturing capabilities, Carbon Steel Casting Company also prides itself on its commitment to quality and customer satisfaction. The company follows rigorous quality control measures to ensure that every product meets the highest standards and adheres to industry regulations and specifications.Furthermore, the company places a strong emphasis on innovation, continuously striving to improve its processes and develop new, cost-effective solutions for its customers. This proactive approach has enabled Carbon Steel Casting Company to stay ahead of the curve and maintain its position as a leader in the industry.The expansion into new markets is a significant milestone for Carbon Steel Casting Company, as it not only opens up new opportunities for growth but also allows the company to diversify its product offerings and reach a wider customer base. With its proven track record of delivering superior quality products and its unwavering commitment to excellence, the company is well-positioned to capitalize on the increasing demand for carbon steel components in various industries."We are excited to announce our expansion into new markets and the introduction of our innovative product line," said [Name], CEO of Carbon Steel Casting Company. "This development is a testament to our dedication to meeting the evolving needs of our customers and our ongoing commitment to delivering superior quality products. We are confident that our expansion will enable us to better serve our customers and establish ourselves as a leading provider of carbon steel casting solutions in new markets."As Carbon Steel Casting Company continues to grow and expand its presence in new markets, the company remains focused on upholding its core values of quality, innovation, and customer satisfaction. With its strong foundation, advanced manufacturing capabilities, and unwavering commitment to excellence, the company is poised for continued success in the industry.
The Importance of Forged Flanges and Fittings in Various Industries
Global Forged Flanges and Fittings Market to Witness Growth in Coming YearsThe global Forged Flanges and Fittings market is expected to witness substantial growth in the coming years. Forged flanges and fittings are critical components in various industries, including oil and gas, chemical, and power generation. These products play a crucial role in ensuring the seamless operation of pipelines and machinery, making them indispensable in industrial processes.One of the leading players in the Forged Flanges and Fittings market is [Company Name]. With a strong focus on quality and innovation, [Company Name] has established itself as a trusted provider of forged flanges and fittings to customers worldwide. The company's extensive product range, which includes weld neck flanges, slip-on flanges, threaded flanges, and socket weld fittings, caters to the diverse requirements of its global clientele.[Company Name] has built a reputation for excellence in the Forged Flanges and Fittings market by adhering to stringent quality control measures and investing in cutting-edge manufacturing technologies. The company's state-of-the-art production facilities are equipped to handle the fabrication of forged flanges and fittings in various materials, sizes, and pressure ratings, ensuring that customers receive products that meet their specific needs and surpass industry standards.In addition to its commitment to quality, [Company Name] also places a strong emphasis on innovation and product development. The company's dedicated research and development team consistently explores new materials and designs to enhance the performance and durability of its forged flanges and fittings. This focus on innovation has enabled [Company Name] to stay ahead of the curve and provide customers with products that deliver superior reliability and longevity.Global industry trends indicate a positive outlook for the Forged Flanges and Fittings market, driven by increasing infrastructure development and ongoing investments in the oil and gas sector. The demand for forged flanges and fittings is expected to be bolstered by the growing need for efficient and reliable pipeline systems, particularly in emerging economies. As industrial activities continue to expand, the adoption of forged flanges and fittings is projected to rise, creating lucrative opportunities for manufacturers like [Company Name].The Forged Flanges and Fittings market is also expected to benefit from advancements in manufacturing processes, which are driving improvements in product quality and production efficiency. As customer expectations for performance and durability continue to rise, manufacturers are investing in advanced technologies to meet these demands. [Company Name] is well-positioned to capitalize on these opportunities, given its commitment to innovation and continuous improvement.The rising focus on sustainable practices and environmental responsibility is another factor that is expected to drive growth in the Forged Flanges and Fittings market. As industries strive to reduce their carbon footprint and minimize waste, the demand for environmentally friendly forged flanges and fittings is anticipated to increase. With its strong emphasis on sustainable manufacturing practices, [Company Name] is poised to meet this growing demand and provide customers with eco-friendly solutions.The global Forged Flanges and Fittings market is highly competitive, with numerous players vying for market share. However, [Company Name]'s reputation for quality, innovation, and customer-centric approach sets it apart from the competition, positioning the company for continued success in the years to come. With the market poised for growth and evolving industry dynamics, [Company Name] is well-equipped to meet the changing needs of its customers and drive innovation in the Forged Flanges and Fittings market.
Durable Forged Metal Hooks for Various Applications
Forged Metal Hooks – An Essential Element in Ensuring Safety and Efficiency in Heavy-Duty IndustriesIn heavy-duty industries such as construction, shipping, and manufacturing, the use of high-quality forged metal hooks is essential for ensuring the safety of workers and the efficiency of operations. These durable hooks are designed to withstand extreme conditions and heavy loads, making them an indispensable tool in a wide range of applications.One company that has been at the forefront of producing top-notch forged metal hooks is {}. With more than 20 years of experience in the industry, {} has established itself as a trusted supplier of these critical components for various heavy-duty applications. The company takes pride in its commitment to providing superior quality products that meet the stringent standards of the industry.Forged metal hooks are commonly used in lifting and rigging operations, where the safety of workers and the integrity of the load are of paramount importance. These hooks are typically made from high-strength alloy steel, ensuring their ability to withstand heavy loads and harsh working environments. The forging process, which involves shaping the metal under high pressure and heat, results in hooks that are incredibly durable and resistant to fatigue and wear.In addition to their durability, forged metal hooks are also designed with safety features to prevent accidental disengagement of the load. These features include latch mechanisms and secure attachment points, providing added peace of mind for workers and operators.A key advantage of using forged metal hooks from {} is the company’s commitment to quality and reliability. By adhering to strict manufacturing standards and conducting rigorous quality control checks, {} ensures that its hooks consistently meet or exceed industry requirements. This dedication to quality has earned the company a strong reputation for delivering products that are reliable, safe, and built to last.In heavy-duty industries, the use of forged metal hooks is integral to maintaining the safety and efficiency of operations. Whether it’s lifting heavy equipment on a construction site or securing cargo on a shipping vessel, these hooks play a critical role in ensuring that tasks are completed safely and effectively. As such, it is essential for companies to partner with a trusted supplier like {} to source high-quality forged metal hooks that they can rely on.With a comprehensive range of hook designs and sizes, {} is well-equipped to meet the diverse needs of its customers across different industries. From standard eye hooks to swivel hooks and shank hooks, the company offers a wide selection of options to accommodate various applications and load requirements. Furthermore, {} also provides customization services to tailor hooks to specific project needs, further demonstrating its commitment to meeting the unique demands of its clients.As heavy-duty industries continue to evolve and demand increasingly robust solutions, the significance of forged metal hooks in these sectors remains steadfast. By choosing high-quality hooks from a reputable supplier like {}, companies can ensure the safety of their workers and the efficiency of their operations, ultimately contributing to the success of their projects.In conclusion, forged metal hooks are a fundamental component in heavy-duty industries, playing a crucial role in lifting and rigging operations. With a steadfast commitment to quality and reliability, {} has solidified its position as a trusted supplier of top-notch forged metal hooks. As industries continue to rely on these critical components, companies can rest assured that they are investing in the safety and efficiency of their operations by choosing {} as their supplier.
High-Quality Forged Parts: A Guide to Understanding Their Benefits and Applications
[Fabrication Company] Introduces Advanced Forged Part Technology [City, State] - [Fabrication Company], a leading provider of high-quality fabricated parts, has recently introduced a cutting-edge Forged Part technology. This new technology promises to revolutionize the manufacturing industry by providing stronger, more durable parts for various applications.The Forged Part technology utilizes advanced forging techniques to create parts that are superior in strength and durability. By using high-quality materials and precision engineering, [Fabrication Company] is able to produce parts that are capable of withstanding extreme conditions and environments. This makes them ideal for use in industries such as automotive, aerospace, and oil and gas, where reliability and performance are of utmost importance.In addition to its exceptional strength, the Forged Part technology also allows for highly intricate and complex shapes to be achieved. This means that [Fabrication Company] can meet the specific requirements of each individual customer, providing them with customized parts that are tailored to their exact needs. This level of flexibility and customization sets [Fabrication Company] apart from its competitors, making it a preferred choice for businesses looking for innovative and reliable solutions.With the introduction of this new technology, [Fabrication Company] aims to further solidify its position as a leader in the fabrication industry. The company has a long-standing reputation for delivering top-quality products and exceptional customer service, and the introduction of the Forged Part technology is a testament to its commitment to innovation and excellence.In addition to its advanced technology, [Fabrication Company] also boasts a state-of-the-art manufacturing facility that is equipped with the latest tools and machinery. This allows the company to streamline its production processes and deliver parts with quick turnaround times, meeting the demands of even the most time-sensitive projects.Furthermore, [Fabrication Company] brings a wealth of experience and expertise to the table. With a team of highly skilled engineers and technicians, the company is able to provide comprehensive support and guidance to its customers, ensuring that their exact needs are met and exceeded.The introduction of the Forged Part technology by [Fabrication Company] is poised to have a significant impact on the manufacturing industry. With its promise of stronger, more durable parts, combined with its unparalleled level of customization and customer support, [Fabrication Company] is set to become the go-to provider for businesses seeking reliable and innovative fabrication solutions.As the industry continues to evolve, [Fabrication Company] remains committed to staying at the forefront of technological advancements. With its continued investment in research and development, the company is poised to introduce even more groundbreaking technologies in the future, solidifying its position as an industry leader.For businesses looking for reliable, high-quality fabricated parts, [Fabrication Company] and its Forged Part technology are the ideal choice. With its unmatched strength, durability, and customization capabilities, the company is poised to set a new standard for excellence in the industry.
Guide to Forging Mold: What You Need to Know
Forging Mold is a vital component in the manufacturing industry as it is used to create various products through the process of forging. It is a crucial tool for shaping and forming metals into desired shapes and sizes. With the advancement in technology and increasing demand for precision and quality in manufacturing, the need for high-quality forging molds has become more important than ever.One such company that has been leading the way in producing top-notch forging molds is {}. The company has been in the business for over two decades and has garnered a reputation for delivering exceptional quality and performance in their products. Their forging molds are widely used in various industries, including automotive, aerospace, construction, and more.The company takes pride in its state-of-the-art manufacturing facilities that are equipped with the latest technology and machinery to produce forging molds that meet the highest standards. Their team of skilled engineers and designers work in tandem to develop innovative and efficient molding solutions that cater to the diverse needs of their clients.In a recent development, {} has introduced a new line of forging molds that boasts of advanced features and improved performance. The new molds are designed to withstand high pressure and temperature, making them suitable for a wide range of forging applications. The company has invested heavily in research and development to ensure that their products stay ahead of the curve and meet the evolving needs of the industry.The new line of forging molds incorporates cutting-edge design and materials to enhance durability and longevity. With a focus on precision and accuracy, the molds are engineered to deliver consistent and reliable performance, resulting in superior quality products. This is crucial for industries where precision and quality are non-negotiable.According to the spokesperson of {}, the new forging molds have undergone rigorous testing and quality checks to ensure that they meet the company's strict standards. The molds have been put through extreme conditions to assess their endurance and performance, and they have surpassed expectations in all aspects.The introduction of the new line of forging molds is a testament to {}'s commitment to innovation and excellence. The company continues to invest in research and development to stay at the forefront of the industry and provide its clients with the best possible solutions for their forging needs. With a focus on quality, reliability, and efficiency, {} is poised to set new benchmarks in the manufacturing sector.The company's dedication to customer satisfaction is reflected in its comprehensive support and services. From design consultation to after-sales support, {} ensures that its clients receive end-to-end assistance and guidance to make the most of their forging molds. This has earned them a loyal customer base that trusts {} for their forging mold requirements.In conclusion, the unveiling of the new line of forging molds by {} is a significant milestone that highlights the company's commitment to excellence and innovation. With a focus on precision, performance, and reliability, {} is set to make a lasting impact in the manufacturing industry. As the demand for high-quality forging molds continues to rise, {} is well-positioned to meet the needs of its clients and contribute to advancements in manufacturing technology.
Improving Product Performance with Alloy Casting
Alloy Casting is a leading company in the field of metal casting, with a focus on providing high-quality, precision components for a wide range of industries. With a strong emphasis on innovation and quality, Alloy Casting has become a trusted partner for businesses looking to source reliable and durable metal parts.The company’s state-of-the-art facilities are equipped with the latest technology and machinery, allowing for the production of complex components with tight tolerances. This has positioned Alloy Casting as a leader in the industry, particularly in the aerospace, automotive, and defense sectors.Alloy Casting’s commitment to quality is reflected in its strict adherence to industry standards and regulations. The company has implemented rigorous quality control processes throughout its manufacturing operations, ensuring that every component meets the highest standards of performance and reliability.In addition to its focus on quality, Alloy Casting is also known for its ability to work with a variety of materials, including aluminum, titanium, and stainless steel. This versatility has allowed the company to take on a wide range of projects, from small, custom orders to large-scale production runs.One of Alloy Casting’s key strengths is its ability to provide turnkey solutions to its customers. From initial design and prototyping to final production and finishing, the company offers a comprehensive suite of services, making it a one-stop shop for businesses looking to source high-quality metal components.Recently, Alloy Casting announced a new partnership with a major aerospace company to supply critical components for a next-generation aircraft. This partnership is a testament to the company’s reputation for excellence and reliability, as well as its ability to deliver on complex and demanding projects.“We are thrilled to be partnering with this esteemed aerospace company on such an important project,” said the CEO of Alloy Casting. “This opportunity is a testament to the hard work and dedication of our team, as well as our ongoing commitment to pushing the boundaries of what is possible in the field of metal casting.”The new partnership underscores Alloy Casting’s position as a trusted and reliable supplier in the aerospace industry, and highlights the company’s ability to meet the stringent requirements and timelines of its customers.Looking ahead, Alloy Casting is poised for continued growth and success, as the demand for high-quality metal components continues to rise across a variety of industries. With its unwavering commitment to innovation, quality, and customer satisfaction, Alloy Casting is well-positioned to continue leading the way in the field of metal casting for years to come.
Precision Die Casting Part: A Cost-Effective Solution for Manufacturing
Die Casting Part: A Crucial Component in Modern ManufacturingIn the world of modern manufacturing, die casting has revolutionized the production process of various metal parts and components. Die casting is a process which involves the use of molten metal that is forced into a mold cavity under high pressure. This results in the creation of intricate and precise components, also known as die casting parts, that are crucial in a wide range of industries including automotive, aerospace, electronics, and more.One company that has been at the forefront of die casting technology is {}. With over 20 years of experience in the industry, {} has been providing high-quality die casting parts to their global clientele. Their state-of-the-art facilities and commitment to innovation have made them a trusted name in the industry.Die casting parts are used in a multitude of applications, from intricate and lightweight components in the automotive industry to complex and durable parts in the aerospace industry. The versatility of die casting makes it an ideal choice for the production of a wide range of components.One of the key advantages of die casting is the ability to create parts with high precision and consistency. The use of molds allows for the production of intricate and complex shapes with tight tolerances, ensuring that each part meets the exact specifications required. This level of precision is crucial in industries where even the smallest deviation can have a significant impact on the performance and safety of the final product.Another advantage of die casting is the ability to produce parts with excellent surface finish and dimensional stability. This is particularly important in industries such as electronics and telecommunications, where the appearance and performance of the final product are of utmost importance. The high pressure used in the die casting process ensures that the molten metal fills every crevice of the mold, resulting in parts with smooth surfaces and fine details.Furthermore, die casting parts are known for their strength and durability, making them suitable for a wide range of industrial applications. The use of high-quality metals such as aluminum, zinc, and magnesium ensures that the final parts are able to withstand harsh working environments and extreme conditions. This makes die casting an ideal choice for industries where reliability and performance are paramount.In addition to its functional advantages, die casting also offers cost-effective solutions for the production of complex metal parts. The ability to create multiple identical parts with minimal post-processing and waste makes die casting an efficient and economical manufacturing method. This is especially important for industries that require high volume production of components without compromising on quality.As a leading manufacturer of die casting parts, {} is committed to meeting the evolving needs of their customers. Their team of skilled engineers and technicians are constantly exploring new technologies and materials to further improve the quality and performance of their die casting parts. By staying at the forefront of industry trends and advancements, {} is able to provide innovative solutions that meet the stringent requirements of today's manufacturing industry.In conclusion, die casting parts play a crucial role in modern manufacturing, offering a combination of precision, durability, and cost-effectiveness that makes them an ideal choice for a wide range of industries. With companies like {} leading the way in die casting technology, the future looks promising for the continued advancement and innovation in this field.
High-Quality Steel Forging Equipment for Sale: Find the Best Deals Now!
Steel Forging Equipment has long been a leading manufacturer in the forging industry, providing high-quality machinery and equipment to businesses around the world. With a commitment to innovation and excellence, Steel Forging Equipment has built a strong reputation for delivering reliable and efficient solutions for metalworking processes.The company offers a wide range of forging equipment, including hydraulic presses, mechanical presses, and fully automated forging lines. With a focus on precision and durability, Steel Forging Equipment has become a trusted partner for businesses looking to improve their forging operations.One of the key advantages of Steel Forging Equipment is its ability to tailor solutions to meet the unique needs of each customer. The company's team of engineers and technical experts work closely with clients to develop custom forging equipment that aligns with their specific production requirements. This personalized approach sets Steel Forging Equipment apart from its competitors and has allowed the company to establish long-lasting relationships with its clients.In addition to its commitment to customer satisfaction, Steel Forging Equipment also places a strong emphasis on research and development. The company continually invests in new technologies and processes to enhance the performance of its forging equipment. By staying at the forefront of industry advancements, Steel Forging Equipment ensures that its products remain at the cutting edge of innovation.Recently, Steel Forging Equipment unveiled its latest hydraulic press, the XXXX series, which has generated significant interest within the forging industry. The XXXX series is designed to offer unmatched precision and control, making it ideal for a wide range of forging applications. With its advanced features and state-of-the-art technology, the XXXX series is set to raise the bar for hydraulic presses in the market.Furthermore, Steel Forging Equipment has expanded its global presence by establishing partnerships and distribution networks in key markets. By strategically positioning itself in regions with a high demand for forging equipment, the company has been able to effectively serve a diverse range of customers and industries.Despite the challenges posed by the COVID-19 pandemic, Steel Forging Equipment has remained resilient and adaptive. The company has implemented stringent health and safety measures to protect its employees while ensuring uninterrupted service and support for its clients. Steel Forging Equipment's ability to navigate through these uncertain times is a testament to its strong leadership and unwavering dedication to its stakeholders.Looking ahead, Steel Forging Equipment is poised to continue its trajectory of success and growth. With a steadfast commitment to excellence, the company is well-positioned to meet the evolving needs of the forging industry and drive innovation in metalworking processes.As a leading manufacturer of forging equipment, Steel Forging Equipment has demonstrated a track record of delivering superior products and services. With its customer-centric approach, dedication to innovation, and global reach, the company is set to remain a prominent force in the forging industry for years to come.